Blog
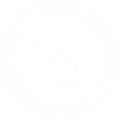
Blog
Some thoughts on Stitching
I get asked to share my thoughts on stitching and pricking irons quite frequently and to highlight the different types and styles out there. The subject is broad and the tools many but I will refer to a few of the most common available.
Much of what I will say is from experience and some is opinion but it is fair to say, my way is not the only way.
Get as much information as you can from as many sources as you can but do not be shy about asking the folks offering that advice to qualify it, and then check it.
There is a lot of misinformation on this here tinter web.
The short version of what I am trying to impart is that leatherwork is not saddlery, as such, different techniques can be used and people will offer advice on what they think you should do, not what works best for you.
I hope this brief insight helps.
The Pricking Iron
The traditional version of this tool if you will.
This is the tool I trained with, Joseph Dixon irons and an awl from Hoopers in Walsall (long gone) and a wooden mallet, how times change. This is a tool designed to prick the surface of the leather marking a row of holes at set distances or SPI (Stitches Per Inch) for the worker to follow. For many years these along with pricking wheels were the only tools used to mark the stitching on leather.
The idea was to only make a shallow hole (pricking) in the leather which acted as a locator for the awl, it was then the awl that made the hole. These irons tend to have flat ends to the teeth which then broadens out up towards the body, if driven in deeply, the hole becomes enlarged and distorted. If just used to prick, a fine slit is left and where the awl comes into play.
Now, we have to know why this technique was used to fully appreciate its use in saddlery.
Just touching on the cobblers stitch for a moment, the cobblers stitch involved a similar way of marking the holes but traditionally, the wheel was the main way of doing so. A large awl was then employed to make a large hole, a hole big enough to allow both needles to pass through at the same time crossing in the hole. This left a larger hole for the thread to sit in, I will come back to that shortly.
In contrast, a saddler, bridle or harness maker looked to make a hole barely big enough to get one needle through at a time. The idea was to ensure that the thread did not ‘ride or slip’ in the hole.
If the hole was too big, the thread would ‘ride’ when the item was in use and if it did, one of two things would happen, the thread, if linen, could fur and snap causing the seam to fail. If the thread was polyester, it would saw at the leather cutting it and the seam would fail. It was, therefore, important to lock each stitch into place to try and prevent this riding and slipping from occurring.
I am sure you can appreciate the dangers of a seam failing on a saddle or bridle when a horse is at full gallop and every seam is being stressed to the max.
So, the secret in this technique was not the iron, it was the awl. The awl blade had a broad body and was tapered to a point, the point was sharp but the body was not. This ensured that the area of leather actually being cut could be kept to a minimum. The awl was then pushed into the hole only as far as it needed to be to get the correct size hole. Just the tip and you have a pinpoint hole, all the way to the haft and you had a much larger hole.
Because the body of the awl blade was blunt, or ‘soft’ the hole was stretched by the awl body, not cut, allowing the stitch to be placed, whereupon, almost immediately, the hole began to close up. This is why only one hole at a time is made and the awl is employed on every stitch as you go.
It is also important to match the correct thread and needles to the iron you are using. This is how some saddlers managed stitching as fine as 18 spi on some pieces. 14 is not uncommon, 12 is a good benchmark.
So… keeping the hole as small as possible ensured each stitch was locked into place and made it ideal for ‘working leather’.
Looking back to the cobbler’s stitch with its larger hole, the stitch did not need to be locked into place as failure was less likely because less ride takes place in a pair of shoes.
Therefor the ‘Traditional Saddle Stitch’ is not just a case of using pricking irons and an awl, it is so much more.
You need to know how to match the iron to the item, the thread to the SPI and the needles to the thread.
Then you need to be able to command the awl whilst wielding two needles, keeping the horizontal and transverse planes accurate, ensure the right angle of the blade is maintained to suit the hole and the depth to push the awl in is the same for each stitch. This is compounded by the fact that the hole on the back is smaller than that on the front, changing the lay of the stitch further still. This technique takes months to lean and longer to master, without doubt, the difficulty here lies in commanding the awl, not the iron.
Some of the pricking irons ideal for this technique are Dixon, Blanchard, Amy Roke, Doldokki, Wuta and Abbey England. Pricking Irons cannot be used as Stitching Irons unless they have very fine teeth or the leather is very thin.
The Stitching Iron
This looks very similar to the pricking iron but the teeth are much slimmer and today, stronger.
They are designed to fully penetrate the leather sometimes up to 6mm. The idea here is to remove the need for an awl and once the holes are made, the worker can go straight to the stitch. Now, however slim the holes appear, they are still bigger than they need to be, in the wrong place, the ‘ride’ can still occur.
The vast majority of people today are making accessories, small goods like belts, wallets, bags and cases. In this situation, the Stitching Iron comes into its own and a seam on a Wallet, Bag, Belt, Case or Box will never be tested as that on a saddle.
I have been a professional leatherworker for over 30 years and teaching these skills for the past 8. I remember when these new irons appeared, my opinion was that they were tat and a gimmick. I was wrong.
A great many people struggle with getting the saddle stitch right when using an awl, I have seen many try and just give up. However, with the irons available today, a fantastic stitch can be achieved, even by a complete novice, in a day. Again, the secret was not in the iron, it was the awl, remove the awl and remove the frustration.
Certainly, now we have a technique totally acceptable for small leather goods.
In addition, a face stitch can be achieved on both the front and back of an item with ease with the new modern style irons. This is more important with small leather goods as it can be examined much easier and turned in the hand. No, it is not as strong or as locked in as the traditional method, but does it need to be? I suggest not.
There are two types of stitching iron: the flat tooth and the diamond tooth. Some companies are calling the flat tooth version the ‘French Style’ and the diamond the ‘Japanese Style’.
Do not be tempted to use the word ‘dent’ unless speaking French properly, it is just a French word for tooth and commonly referred to when talking about round tooth irons. No French company has ever made round tooth irons to my knowledge.
The Flat Tooth version irons leave a slit in the leather the width of the tooth and very narrow, for small leather goods, these give a very pleasing stitch and I use then for teaching here in the workshop with great success, I believe they have made good leather work more attainable for more people.
A few good makes of flat tooth Stitching iron are KS Blade Punch, Crimson Hides, Kevin Lee, Amy Roke and Sinabroks.
The diamond tooth version of the stitching irons also have their place, these leave an even bigger hole so are definitely to be avoided if working Tack. The larger hole suits a larger thread, are much easier to stitch with and suit a thick or difficult leather. Either way, they are still designed to fully penetrate the leather fully so fall under the title Stitching Iron.
These types of irons are available from Crimson Hides, Kevin Lee, Doldokki and KS Blade Punch.
Stitching irons can be used as pricking irons.
Stitching Chisels
Whilst I have many of what are termed Stitching Chisels, I cannot be sure where the term was coined. They are in essence, a more basic version of Stitching Irons. We know a chisel is a tool for woodwork so I think it may have been a crossover in translation. Still, they work the same way, they are designed to fully punch through the leather making a hole without the need of an awl so you are ready to stitch straight away.
The teeth tend to be long, straight and very thick and leave a large diamond shape hole. The biggest issue with these tools is that the edges of the teeth tend to be quite sharp, so the hole you make is the hole to are left with, it will not close up well so not suited to more adept leather workers. I have found them ideal for absolute beginners as the large hole they give makes it very easy to get the needles through and therefore stitch. People often get the balance wrong when stitching and have to resort to pliers, these definitely will avoid that.
Some common makes of Stitching Chisels are Tandy, Seiwa, Craft-Sha and Craft-Tool.
Leaving off the chisels for the time being, I would put the irons into two brackets: Traditional and Modern.
The Traditional is the stitch attained using a pricking iron and awl and the modern is that using the Stitching Iron and no awl.
There will always be a place for an awl so practice is encouraged, even with the modern style.
This is designed to complement the iron reviews on my YouTube Channel, Armitage Leather. So far there are about 20 and more will be added in time.
I shan’t add the individual reviews here, you have access to the info sheet and the videos. But opinions are valuable, add yours.
Unless of course you include stitch grooving or drilling holes. Then you will be sat in a corner.
I will leave you to discuss, dissect and question. Always question.
If you struggle with your stitching, I cover both styles, left and right-handed on my Vimeo Channel and run courses here in the workshop.